Importing CAD Geometry
The first thing to do is import the CAD geometry. To do that, go to File > Import > Geometry and then select the geometry file you want to import.
File>Import>Geometry:
Scale factor is 39.97 to convert meters to inches
Set the geometry scale factor to 39.37 because the geometry is in meters and we want our graphic to come in inches.

Measure the first geometry imported into FEMAP to verify that the scale factor was set properly
The imported geometry comes into the active layer.
Isolate the geometry that will be using for meshing (in this case, the grey solid). To do so, create a new layer that the geometry will go into. (We named ours “Bracket Solid”)
Geometry Manipulation
The next thing to do is prepare the geometry for mid-surfacing. As you can see, it has fillets, holes, and other things that we don’t want to model.
Removing Holes
First remove the small holes around the larger holes. They are not necessary to represent the structure.
Move to the loops command. To remove the holes, just select any curve on the circle.
Note how all small holes are removed!
Removing Fillets
Next remove the fillets. The fillets are going to cause issues with the mid-surfacing tool.
Go to Feature Removal > Surfaces.
To remove fillets properly, you have to select all the surfaces in a loop. Otherwise you could run into errors with the geometry modification.
Continue to select all the surfaces in one continuous loop. If you want to check the surfaces that you have selected, you can highlight it; showing clearly the surfaces you have selected.
Click OK and it will remove all those surfaces, leaving nice sharp corners. Repeat this step to remove all unnecessary fillets.
Now that all the fillets in the model are removed, we are ready to start mid-surfacing.
Midsurfacing
Create a new layer to put the surfaces into (we named ours Bracket Midsurfaces) and turn the layer on.
Next perform the mid-surfacing command by going to Geometry > Mid-surface > Automatic. Select all the surfaces on the bracket. To determine the target thickness, you can measure the thickness of the bracket. Since most of the thicknesses on the bracket are similar, we just measured one area and selected a target thickness of 0.2 inches.
Select “Combine Midsurfaces” so that it will combine all the surfaces it creates into one solid, allowing us to avoid any coincidental curves.
Now that the surfaces have successfully been created, they can be viewed by turning off the Bracket Solid layer, leaving the 2D surfaces that were created.
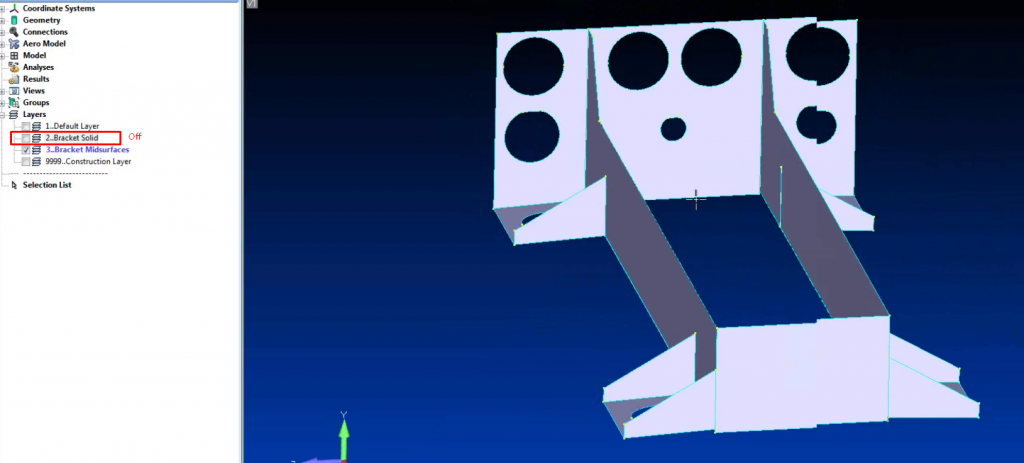
Checking Free Edges
Check the free edges on these surfaces just to make sure that it performed correctly. To do that, go to the Meshing Toolbox. Turn on the “Toggle Entity Locator” and select Free Edges.
As you can see it created some free edges where we don’t want them.
Zoom in to see what the mid-surfacer did. As you can see, it created a sliver surface that we’re going to want to get rid of, and messed up the end of the foot. We’re going to get rid of those surfaces and recreate them.
Correcting Free Edges
First select and delete those surfaces.
Now recreate those surfaces by going to Geometry > Surface > Corners.
Select the corners of the surfaces you want to create.
Next add the circles back by projecting them onto the surface.
First project the curves from the solid onto the surface. To do that go to Geometry > Curve – From Surface > Project and select the surface. Then select the curves you want to project onto that surface.
We also want to do that to the bottom to create our property regions for the bottom surface. Redo the command Geometry > Curve – From Surface > Project. Now the circles on that surface can be deleted.
Now that the surfaces have been created, add them to the solid of the rest of the bracket.
To do that, use the non-manifold add command. Geometry > Surface > Non-manifold add.
Select the surfaces. When you perform this command it will display the free edges, showing that we no longer have the unwanted free edges.
Creating Meshing Surfaces
Breaking Up the Surfaces
Now we’re ready to start breaking these surfaces into meshing surfaces. Go to the Geometry Editing tab under the Meshing Toolbox. We will start at the feet.
Meshing around a hole can prove challenging. One of the geometry meshing tools that makes this easy is the Pad command.
Using the “select”, select a curve on any circle and it will create a pad around that circle that will create a math-mesh, creating a nice circle. Repeat the pad command on all of the feet.
Continue breaking up the surfaces into meshing surfaces by using to the point-to-edge command. This is good for creating more rectangular surfaces, which are good for meshing. It can then be broken up further by using the point-to-point command.
Determining where you want to break up surfaces will come from experience and trail-and-error.
Meshing
Now that the surfaces have been broken up, we’re ready to start meshing. The bottom has a variable thickness so we will create multiple property regions with varying thicknesses.
First create the material and property regions. Create a new material and load one in from the FEMAP presets. (We chose aluminum 7050)
Next create 3 properties. First property with a thickness of 0.2 inches, second property with a thickness of .375 inches, and the third property region with a thickness of .225 inches.
To begin meshing, go to the meshing toolbox and select the mesh surface command. From here we can select the property we want to start meshing with (the 0.2 inches property).
Set the mesh size to 0.2 inches. Select Mapped Mesh and choose the Auto Mapped Approach. Use the select tool to select the surfaces to mesh.