Setting the Material
First, we'll create the material data (aluminum alloy in this case). Follow these step-by-step instructions:
- To create a material, expand model tree in FEMAPs model info pane and right click on the material object.
- From the context sensitive menus select New.
- Note that's in the defined material dialog box, you can change the material type from the default isotropic to one of the many material types supported by FEMAP.
For this model we’ll select an aluminum alloy from the extensive metal alloy material database included with FEMAP.
Selecting the material in the model info pane sends the material data to the entity info pane for reviewing and editing if needed.
Element Properties
To create an element property, follow these steps:
Right-click on the property object in the model info pane and select New.
To change the property type to a solid from the default plate element type, click the element property type button in the defined property type dialog box and set the element type to solid in the element property type dialog.
Select the material that we defined previously for the solid element property and supply a descriptive title to complete the property creation.
Loads and Constraints
Now we will define the loads and constraints which can either be applied to geometry or directly to a finite element mesh in Femap. Femap manages different boundary conditions through the use of load and constraint sets which can be combined, and for loads, can also be scaled. To create a load set, follow these steps:
- Right click on the loads object and select new.
- Enter a descriptive name for the load and click ok.
- Expand both the loads and the newly created load set objects.
- Right click load definitions and select on surface from the menu. Note that you can select through the parts to select the services that the load is to be applied to.
- You can select the preview button in the entity selection dialog box to highlight and check what you've selected before clicking OK.
- In the create loads on surface dialog box, add a title and change the load type to bearing force.
- Enter a value for the bearing load (which in this case is five hundred).
- Deselecting the normal to surface option changes the load from radial to directional.
- After clicking OK we'll define the direction of the bearing load.
- To change the vector direction from the default start and end of the vector, click the methods button and select components.
- In this case the base of the vector will be the center of one of the arcs on the hole at the top of the arm. Clicking the preview button will generate a temporary display of the vector, using the values in the dialog box.
- The components we want are .5 for dX, -.25 for dY, and -1 for dZ. By expanding the load definitions object and selecting a load, we can check that the load application is correct.
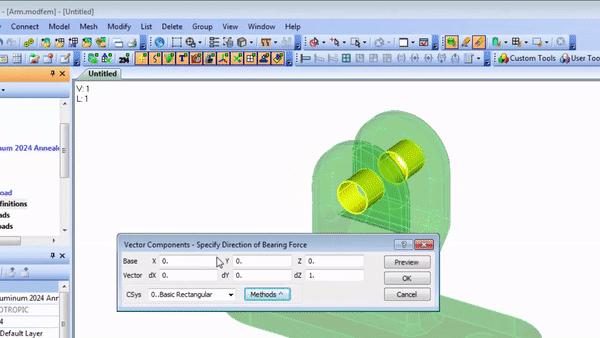
- We'll now apply a pin constrain on the holes at the bottom of the arm.
- Just as we did to create a load set, right click on the constraints object and select new.
- After entering a descriptive name for the constraint sets.
- Click OK to complete set creation.
- Expand both the constraints and the newly created constraint set objects in the tree.
- Right click constraint definitions and select on surface from the menu.
- Select the four surfaces that comprise the two holes at the bottom of the parts.
- In the create constraints on geometry dialogue change the type to pins before clicking OK.
- Selecting the constraints in the model info pane, you can highlight the geometry and check the constraint definition.
In the next section, we'll move on and mesh the geometry to create the finite element model. Then we’ll set up the analysis parameters and output requests for the next NX Nastran solver.