One of the most important parts of a stress analysts job is checking their work. Usually this is learned via trial by fire, and after making enough mistakes, a green analyst gains experience eventually learns what to look out for. Here are 5 mistakes that are very easy to make, but also quick and easy to check for:
- Free Edges
- Using an RBE2 instead of an RBE3
- CBUSH Mis-oriented
- Shorted Out CBUSH
- Incorrect Units on Material Density or Mass Element
1. Free Edges
Free edges are locations where a mesh touches another mesh but isn’t actually connected. Its easy to forget to check for free edges when quickly meshing up some geometry or iterating, but it can cost a lot of time if the whole analysis is carried out and the free edge is only caught at the end. Free edges can enter a model during at two different stages:
- Geometry preparation
- Mesh modification
Geometry Preparation
When midsurfacing a part, its common to end up with separate surfaces that need to be united together so that mesh on intersecting surfaces matches up and shares common nodes. This is commonly accomplished with the “Non-Manifold Add” command. Usually there is no problem, but there are certain situations where it might fail silently only for you to discover a free edge after running the analysis.;
Heres an example. In this model there are two separate plates (separate solids) that intersect at an edge. If they were meshed now, they would not be connected.
By using the command Geometry>Surface>NonManifold Add, these two surfaces can be joined together and their mesh will match up and be connected when meshed.
However, sometimes, this command might not catch all intersecting surfaces, especially when dealing with curved surfaces that might not perfectly touch. Conveniently, when you use NonManifold Add, it shows a free edge plot after joining everything together. This is a great way to check to make sure all the edges are merged together. If not, you have several options to resolve:
- Undo and change the tolerance and/or processing method
- Undo and change the geometry
- Geometry>Midsurface>Extend to create a true intersection between the surfaces (you can delete the excess sliver surfaces after NonManifold Add)
- Try to recreate the surface using a different method (instead of midsurface automatic, try Geometry>Midsurface>Single in Solid etc.)
Locate Free Edges
If you have geometry that you just need to check for free edges, the Meshing Toolbox's Locator tool can help do free edge checks without needing to run the NonManifold Add command. There is a lot of other functionality in this tool that is worth exploring.
Used on this simple model, it shows that the shared edge on this part is actually two separate edges.
After a NonManifold Add command, it should un-highlight the shared edge.
2.0 Accidentally Using an RBE2 Instead of RBE3
This is probably one of the easiest mistakes to make, and it has huge consequences. Since RBE2s are infinitely stiff, using them in place of what should be an RBE3 element (that adds NO stiffness) is obviously a huge difference, especially since RBE3s are usually used to spread mass over potentially large areas.
How It Happens
- Since the FEMAP RBE creation dialog defaults to RBE2, it is easy to forget to change the tab when creating what you think should be an RBE3 element.
- It is also easy to "Convert" an RBE3 to an RBE2 (if, for example you're modifying the list of leg nodes) but then forget to to change back to an RBE3.
- Furthermore, because the default coloring for both elements is white, it is also not immediately obvious which elements in FEMAP are RBE2 and RBE3, especially model that you did not make!
Catching the Mistake
Fortunately it is also very easy to check for by using one of the built in FEMAP API's in "Custom Tools" drawer. By turning RBE2s red and RBE3s blue, you can visually identify if they are used properly.
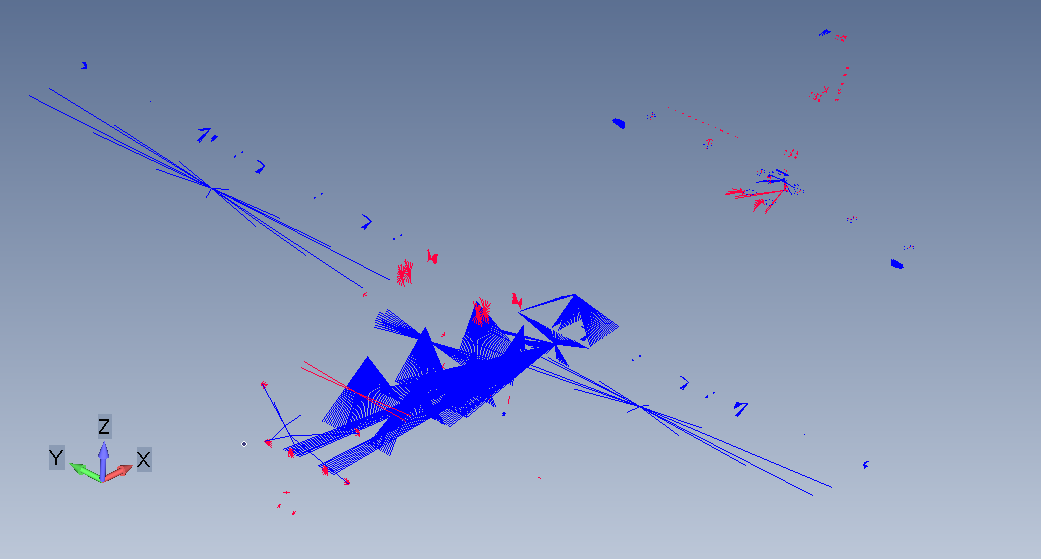
The user can now quickly identify whether there are any large red RBE2s present in the model and if they are an issue.
3. CBUSH Misoriented
Ask a few analysts, "What axis should be the tension direction on a CBUSH element?" and you are likely to get two different answers:
- "The X direction - because this follows the NASTRAN convention for a nonzero length CBUSH which defaults to X aligned from node1 to node2"
- "The Z direction - because shear should be in the XY direction. Also, Z sounds more like an out of plane load."
Hopefully no one says bolt tension belongs along the Y axis! This convention is usually set by program management (not by the FEMAP program), but it is always possible for a green engineer to pick their favorite or have a consultant use their preferred axis.
Whether you use X or Z, it is important to keep track of this in your models because it will determine which output vector will is treated as "Tension" and which vectors will be treated as "Shear". Mixing this up in the model will affect loads processing downstream when one of the shear direction loads is treated as tension, and the tension load is RSS'ed with the other shear direction load. Then you'll be wondering why there is so much tension on a joint that is supposed to be primarily taking shear.

For fasteners, it is customary to "release" (set to low stiffness) the drilling degree of freedom (the moment stiffness along the axis of the bolt - think of this as trying to spin the bolt). This can help you identify the tension direction.
Catching the Mistake
Fortunately this is also very easy to check for by using another Custom Tool, "Show CBUSH CSYS".
This API will create CSYS arrows according to the orientation of each CBUSH in your model.

This API creates GFXArrow objects on Layer 1 by default. In a large model that is sorted by layers, it is more convenient to have these objects placed in the same layer as the element that they represent. Try modifying the Custom Tools API as a challenge!
Checking the property card, the drilling release is along the Z axis, meaning that bolt tension is also along the Z axis. Checking the axes drawn on the lug fasteners, this matches the assigned orientation. It is up to the analyst to remember/track that this fastener has tension oriented along Z when processing fastener loads.

To remove the GFXArrow Objects, simply run the "CBUSH CSYS Display Reset" command from the same folder.
4. Shorted Out CBUSH
One of the most frustrating things to find is a shorted out CBUSH, where the elements on either side of the CBUSH are directly connected together, bypassing the CBUSH element. The CBUSH reports ZERO load and this joint will also completely ignore any releases specified via the CBUSH stiffnesses assigned.
How to Check
Run a 1G Check, export all CBUSH loads to Excel, and sort by CBUSH with ZERO load
Write a custom API that checks each CBUSH for nodes not connected to anything else (freestanding nodes), which would indicate it is shorted out
How to Fix
Unfortunately, this is something that is hard to fix automatically. The only way to fix is to delete the connection and redefine.
Alternatively, it is possible to Mesh>Connect>Unzip the two elements on either side of the CBUSH and then update the CBUSH to reference the new node created.
5. Incorrect Units on Material Density or Mass Element
When working in slinches or megaTons, it is easy to input the density using lb or kg by accident, especially since datasheets are usually in these units. Since this is off by several orders of magnitude, it should be readily apparent after model run, however its always better to catch these things beforehand.
How to Check
The easiest way to check material density or mass assigned to a mass elemetn en masse is to list materials to the data table via the Selector toolbar. If it is not in your GUI, right click anywhere in the menu bar, and click "Select" from the drop down to add it.

- Activate the Data Table (if you don't, the data will not be sent)
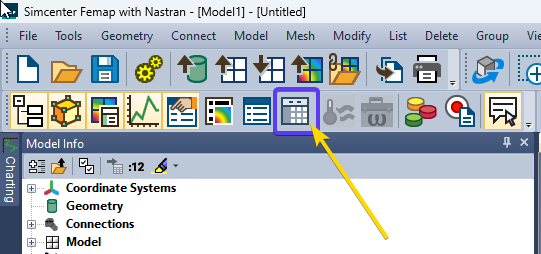
- Pick "Materials" (or property, if checking Mass elements) from the Selector toolbar "Selector Entity" drop down
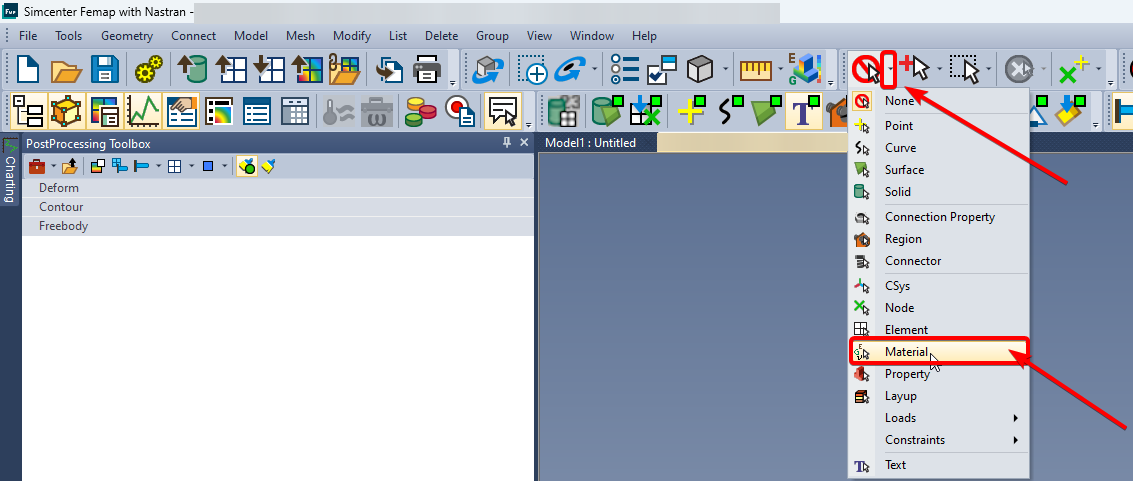
- Change the "Selector Mode" drop down to "Select Multiple"
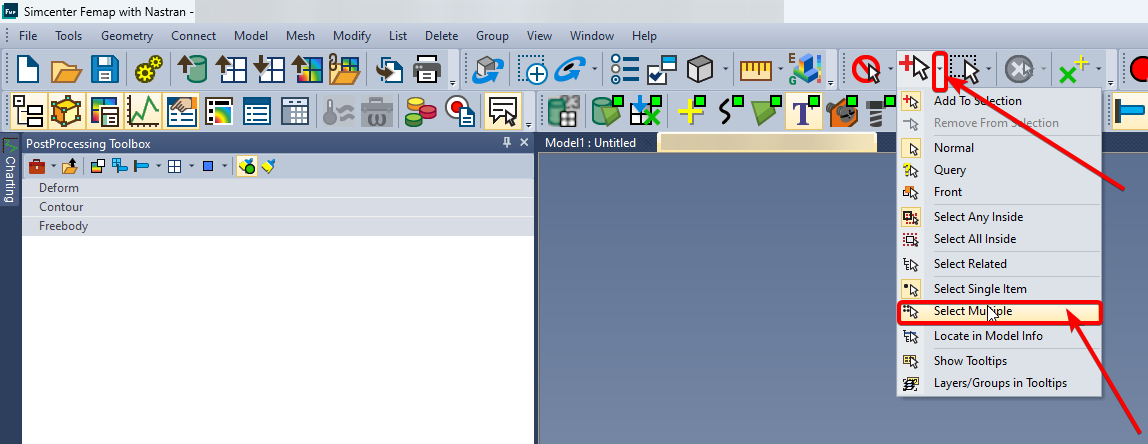
- Make sure the data table is open and select from the "Selector Actions" drop down: "Dialog..." which should bring up a material selection dialog (or the property selection dialog if checking mass elements. Pick by type, "Mass" if so). Click "Select All" and Ok.
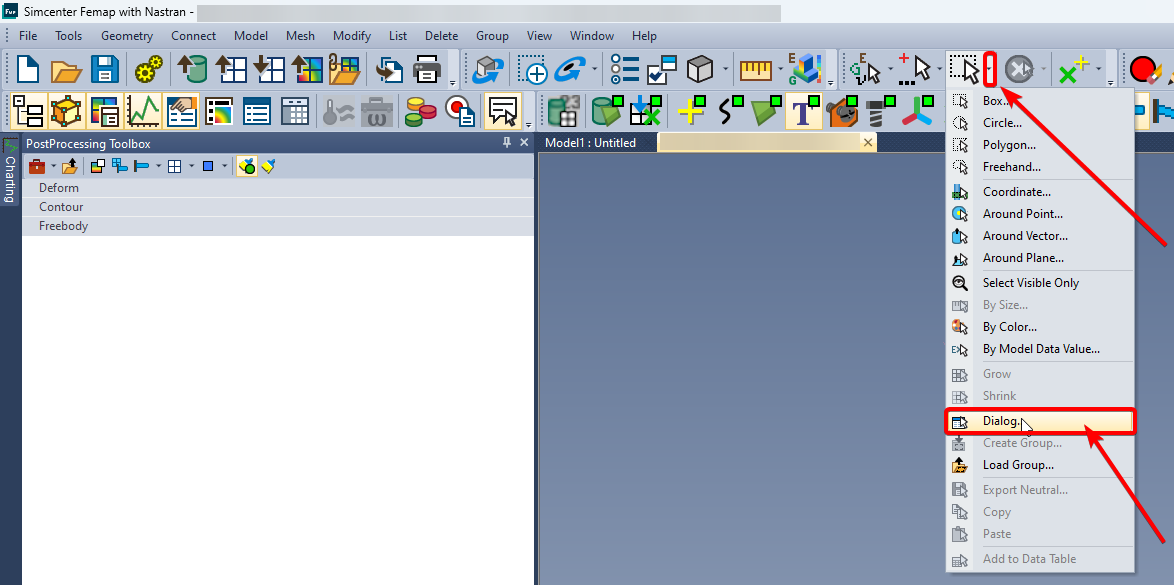

- The data table should now be populated with all the material data in the FEM. Click on the "Density" column to sort by density and it should be fairly clear if there are any values entered wrong since they would likely be off by 2-3 orders of magnitude.
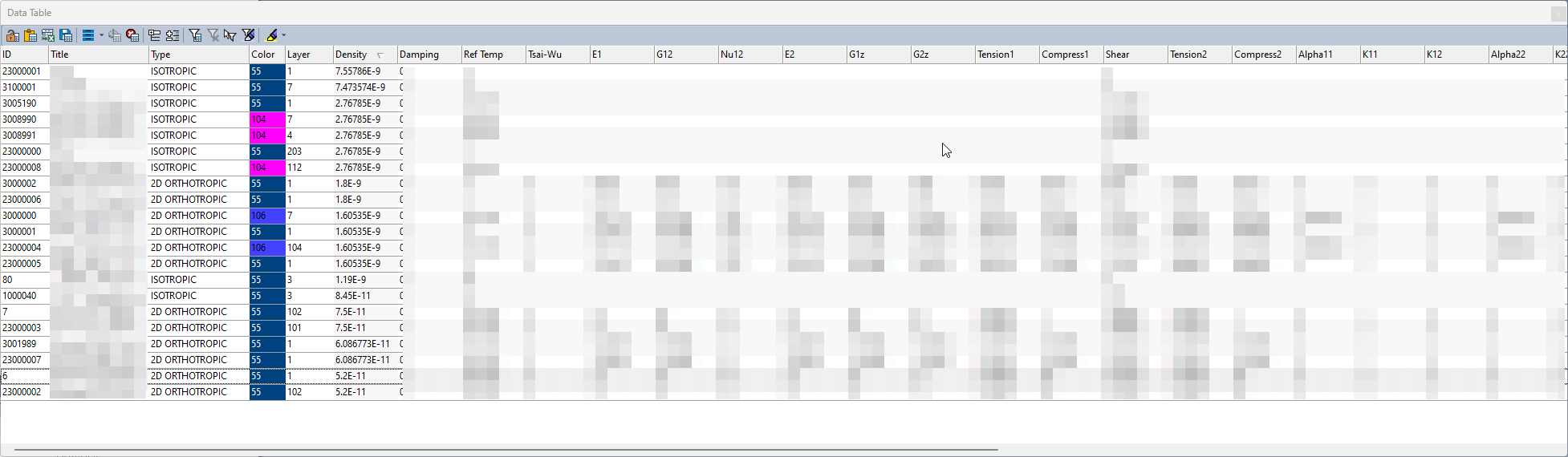